High-quality sputtering targets
High-quality sputtering targets thanks to flash sintering
SINTERMAT produces high-quality sputtering targets for physical vapor desposition (PVD) thanks to flash sintering.
What’s a Physical Vapor Deposition (PVD) ?
To begin with, Physical vapor deposition (or PVD) is one of vacuum thin-film material deposition techniques. This process enables the transfer of an atomic-state material, from a sputtering target onto a single part.
The target material is striped off in a high vacuum by means of an intense energy source.
Then, the material is deposited on the surface of the part, in the form of thin and uniform film.
This deposition method offers several advantages for the coated material. Among these are : high hardness, resistance to wear, to corrosion and also durability and resistance to high temperatures.
In addition, the PVD coating process is environmentally friendly without pollutant release during the deposit phase.
Moreover, the deposition method can enhance the aesthetics of the coated part through its choice of colors.
Thanks to these advantages, PVD is particularly well suited to these applications : aerospace, medical, automotive, electronics, industrial toolings and luxury goods in particular.
There are various physical vapor deposition methods :
- thermal evaporation (joule effect)
- cathode sputtering
SINTERMAT produces sputtering targets suitable for magnetron sputtering. This sputtering process enhances cathode sputtering with a magnetic field. The latter acts on electron trajectory and their ionization capacity to improve coating quality.
Sputtering targets for PVD coating
What’s a sputtering target ?
A sputtering target is a term used to describe the material to be sputtered by physical vapor deposition. When vaporized, this material is deposited on the surface of the object to be coated, in a thin layer.
The sputtered target is made up of the material to be deposited on the substrate (part to be coated). Most importantly, this target must be designed with materials of excellent qualities, high purity and adapted to the substrate.
How important are sputtering targets for PVD coatings ?
The sputtering target is an essential component of the physical vapor deposition process.
In fact, the material constituting the target determines the final coating. In other words, an aluminum sputtering target will produce an aluminum coating, a titanium sputtering target will produce a titanium thin-film deposit etc…
A wide range of materials can be used as long as they are pure and of high quality to ensure coating quality.
The coating quality enables us to propose parts that meet the requirements of electronic, automotive, aerospace, industrial medical devices or luxury goods.
Flash sintering produces sputtering targets with unique characteristics
With spark plasma sintering (SPS) process, SINTERMAT offers high-quality sputtering targets.
Indeed, this technology allows production of high density materials and favors a reduced grain size.
It is used to sinter a wide variety of materials including ceramics, composites and metals.
Furthermore, targets produced in this way present higher performance thanks to their high density and fine microstructure.
Thanks to our process and our know-how, unique in Europe, the quality of our targets brings added value to many customers :
- density equal or close to 100 %
- material types available : WC, B4C, SIC, P3N5…
- deposition rate up to 20 % higher than competing materials
- conditioning time much shorter before the first coating process
- coating produced in line with customer specifications
The flash sintering process offers the advantages, in particular, of rapidity and controlled temperature rise along with speed of cooling.
To sum up, this enhances the properties of the sputtering targets proposed by SINTERMAT.
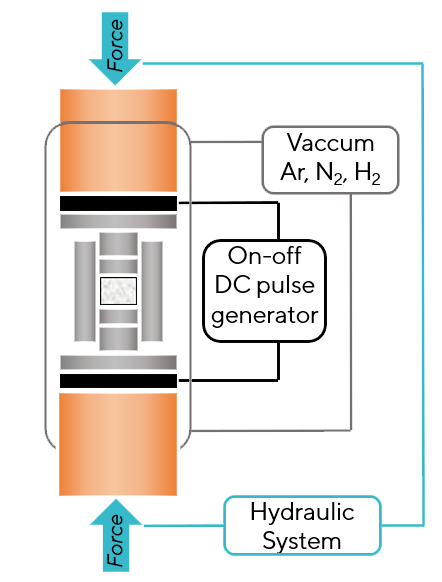
Mechanical properties
Fine microstructures
The control of temperature rise and speed of cooling provide mechanical properties superior to those produced by conventional processes.
Thanks to flash sintering, the increase in grain size is limited, guaranteeing a fine and homogeneous microstructure of the materials to be sprayed.
Wide range of materials
The SPS process can be adapted to many types of materials, and so enables the production of sputtering targets with enhanced properties of many kinds : ceramics, cermets as well as metals, metal oxides, metal carbides…
Technical data for SINTERMAT sputtering targets
The know-how of our teams enables us to propose you custom-made sputtering targets with the following characteristics :
- available target diameters : from 10 to 350 mm,
- available target thicknesses : from 2 to 10 mm (up to 80 mm depending on diameter),
- available classic shapes : round / square / rectangle. Other Formats are available under conditions (Near Net Shape),
- available digital support : thermo-electric and thermo-mechanical simulations (thermal and mechanical mapping).
SINTERMAT produces sputtering targets in a wide range of materials
Thanks to its innovative flash sintering technology, SINTERMAT produces sputtering targets with unique properties in a wide range of materials.
SINTERMAT offers its customer high-quality and high-purity sputtering targets for production of PVD coatings, meeting the requirements of various companies.
In addition, flash sintering offers real benefits for ceramic targets of the SIC or B4C type, which are denser and less prone to fracture.
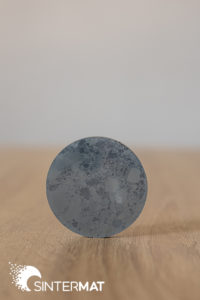
How important are sputtering targets for PVD coatings ?
Properties of ceramic sputtering targets include resistance to high temperatures and thermal shock, as well as excellent mechanical properties. We can also mention hardness, corrosion and wear resistance.
Few examples of materials we master :
- Tungsten carbide : WC
- Silicium carbide : SiC
- Boron carbide : B4C
- Chromium carbide : CrN
- Titanium carbide : TiN
- Alumina : Al2O3
- Precious metals : gold, silver, palladium… etc
SINTERMAT assists a large number of manufacturers in the creation of innovative materials : luxury goods, aeronautics, defense, tooling, energy…
SINTERMAT supports manufacturers by supplying innovative materials thanks to its mastery of the spark plasma sintering process. These materials meet the most demanding specifications in the aerospace and security/defense sectors. These materials are also a response to orders for complex, high-performance parts from the industrial and energy sectors, as well as the most elaborate designs from luxury goods manufacturers.
Sputtering targets with Sintermat
From the quality of raw materials to the control of finished products, SINTERMAT team has the human and technical resources to guarantee the quality and repeatability of the parts produced. As an illustration, thanks to the team’s expertise, raw materials are carefully selected depending on their technical qualities and their suitability to the technical characteristics required by the finished product.
The various production parameters are precisely controlled to guarantee the quality of the material produced by SPS sintering.
Whatever your business sector, prediction, analysis and modeling the behavior of your products in their environment is a guarantee of technical mastery, quality and cost reduction.
Digital simulation has become the essential initial step in any successful new development. Consequently from the initial draft to the commissioning of your product, our expertise and calculation tools will support you throughout your research, development and innovation project.
SINTERMAT team's expertise
Thanks to his expertise, the SINTERMAT simulation team can support you in :
- simulation of your product behavior during all phases of design and manufacture,
- analysis, detection and correction of production line anomalies,
- optimization of manufacturing costs through experimental plans,
- provision of fast, powerful calculation tools.
What’s more, we offer you a single point of contact to support your research and development. Otherwise, thanks to its skills, our team gives you access to a multidisciplinary field of expertise (metallurgy, defense, aeronautics etc…).
Finally, the ISO 9001 certification obtained by SINTERMAT certifies reliability, quality and repeatability of our various manufacturing processes, to achieve full customer satisfaction thanks to our continuous improvement procedures.
Have you got a project ?
Do you want to offer innovative products and unique materials to your customers ? Would you like to improve your parts ? Do you wish you could recycle your production scrap ? Contact us today.